Common Loopholes in ERP Manufacturing Software
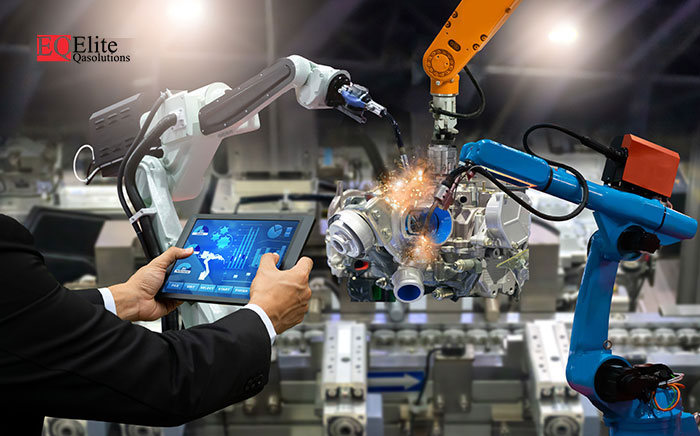
A company’s ERP manufacturing software is an integrated system that clubs all the departments of your organisation together and ensures they work in a single methodological manner. In the manufacturing sector, it helps companies accomplish smooth functioning of dedicated operations that involve manufacturing, service delivery, marketing, sales and inventory management. There are numerous day to day reports and data accumulations in the form of repositories that needs to be managed. The ultimate aim is to have a smooth system that delivers an easy and uniform flow of information under clearly defined codes and procedures. A successful ERP system implementation requires continuous system testing that helps identify loopholes and ensure quality is delivered throughout the business processes.
To define:
An ERP or Enterprise Resource Planning system refers to a combination of software and systems utilised for planning and managing all the core supply chain, manufacturing, financial and other essential business processes for an organisation.
The annual growth rate of the Global Enterprise Resource Planning (ERP) market is expected to grow from USD 45.3 billion in 2020 to USD 101.1 billion by 2025, at a Compound Annual Growth Rate (CAGR) of 17.4% during the forecast period, as per the forecast of MarketsandMarkets.
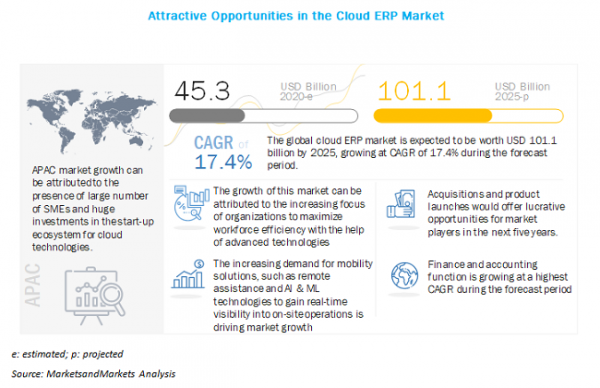
One of the most crucial elements of a successful ERP implementation is a well-planned and well-executed performance testing model. It’s necessary to validate your system’s state in a real-life production environment and identify its stability. To get the desired results, testing software within the production environment is a crucial step. Skip this and the next thing you know is getting user-escalated issues within your system or worst, the security of your vulnerable systems compromised. It’s extremely crucial to coordinate and execute a stress test before going live. These are the areas where outsourced performance testing services can come in handy as they ensure you focus on your direct business requirement and leave the quality assurance to an expert.
As of today, even the smallest of companies have realised the relevance of a comprehensive ERP system within their processes. The various possible reasons an ERP solution can fail include:
- Zero testings before go-live
- Wrong target audience while crowd testing
- Incorrect methods of testing
Talking about a manufacturing industry specifically, with large size companies and over thousand-odd employees scattered across the globe, they face numerous operational problems in their day-to-day operations. In this blog, we will closely monitor the above ERP implementation loopholes along with others that can easily be avoided with the right amount of planning and execution strategy in place.
Let’s start with why you need ERP manufacturing software altogether.
Why do you need ERP Manufacturing Software?
Many small businesses at times may not require a strong ERP system at the beginning of their operations, but as the size of the organisation grows and more stakeholders come into the picture, implementing an ERP system becomes inevitable.
Here are six reasons you should consider using a new ERP:
1. Centralize Data
The ability to manage all your business processes from a single centralised digital platform is one of the major benefits of an ERP for a manufacturing enterprise. Looking at the size of an enterprise, most manufacturers have subdivided processes that include manufacturing, accounting, shipping, financials, human resources and more.
Businesses manage a lot many functions separately, which are likely to be exposed to many challenges that include data errors, duplication of functions, miscommunication etc. All these issues can be curbed with an efficient ERP solution in place.
2. Real-time Project tracking
Real-time inventory tracking is one issue that most manufacturers struggle with. A few of the major consequences of this can be higher expenses, insufficient storage space due to excess inventory, and low productivity due to insufficient inventory, among several others.
A strong and well-established ERP system allows managers to have a grip over these functions and monitor the progress of any project in hand, all in one place. Issues like delays in deliveries and urgent product requirements can be addressed immediately along with reliable analytical reports from real-time data management.
3. Better Budgeting
One of the most significant key drivers for the adoption of a new ERP solution is cost reduction. After successfully implementing an ERP system within your organisation you get updated and real-time records of the functioning of your operational systems that ultimately reduces your administrative cost to a significant per cent.
4. Improved Productivity
A well established and integrated ERP system helps your enterprise to eliminate redundant processes that can be easily handled by automated software. Processes that can take forever to be accomplished otherwise. It covers regular tasks like generating reports, maintaining inventory, employee timesheet tracking, etc. that are simplified on a day-to-day level, ultimately resulting in improved productivity.
Read to Know How World’s leading Crane Manufacturing Company Streamlined Business Processes and Increased Process Efficiency by 45%
5. Better Client Handling
ERP systems allow your sales teams to analyse the shifting interests of your clients more holistically that can help you build better sales strategies for improved lead generation. Furthermore, it allows your teams to keep your clients in the loop with the progress of your project in hand with updated real-time data shared at equal intervals.
6. Better Features
With the ever-changing digital transformations in place, ERP solutions come with the latest technologies and updated software systems, customised for the individual needs of your customers – another strong reason for you to opt and implement an ERP system. Examples include Machine Learning (ML), Artificial Intelligence (AI), Data Analytics (DA), and the Internet of Things (IoT), all integrated to deliver the necessary ease of business required in your organisation.
Common Loopholes in ERP Manufacturing Software
Having understood a few of the many reasons you need to implement a new ERP system in your business processes, let’s take a further look at some of the most common ERP implementation loopholes that must be avoided by any manufacturing company.
1. Inaccurate Planning
As mentioned, a couple of times in the above sections, inaccurate requirements gathering and no proper planning can result in a total failure of your ERP implementation. Noting that one of the most essential ingredients of a successful ERP implementation is automation, the fact that its effectiveness depends majorly on the processes it automates cannot be overlooked. Automation in itself comes with a lot of challenges that are needed to be addressed. Therefore, automating an outdated and inefficient process makes it run faster and improves your overall efficiency.
2. Ignoring the End-Users from the Decision-Making Process
It is important to note that the major end-users of your ERP system are not just the C-level executives but the rest of the organisation as well. Ignoring to take appropriate inputs from all these executives can lead to misunderstanding and operational complications. Departments like finance, operations, manufacturing and warehouses are needed to be looped into an organisational level change like this to ensure an easy and smooth transition.
A smooth and effective change management system is the key here. Making a list of all those employees who will be affected by this change, ensuring proper hands-on training are all essential parts of this system. The change needs to be managed at three key organizational areas: people, process and technology. The people factor here requires intensive planning, strategizing and execution to avoid last-minute failures.
Also Read: Top 5 Tips for Successful ERP Implementation Testing
3. Inadequate Budgeting
Enterprises often underestimate the overall cost of planning, strategizing and executing a big move as ERP implementation into their organisation. It’s not just the cost of implementations but the after training and maintenance cost that can take a toll on your overall project budgeting if not calculated comprehensively. Major blunder organisations make is by trying to achieve more with less or inadequate resources that end in total project failures.
4. Go Live in One Go
Many technical experts still believe that the implementation of an ERP system is more like a traditional waterfall model. On the contrary, what needs to be understood here is the need to incorporate a more agile system of implementation with modern technological solutions. An ERP system is complex and it may not be easy to determine all the implementation requirements in one go. Moreover customising, integrating and training also takes time and close monitoring. Taking baby steps along with a reliable ERP implementation service provider is the key to this journey.
5. No Maintenance Plan
Implementing an ERP solution is one part of the system and responding to user escalated issues and fixes is another. Having a proper maintenance plan that includes a customer success team that addresses your employees’ issues from time to time is necessary to help improve the system to a level that suits every single element of your business processes.
How can we help with your hassle-free ERP implementation journey?
Many say implementing ERP software is a once in a lifetime move for any enterprise within an organisation. On a contradictory note, it’s more of an ongoing journey towards an updated, integrated and collaborated functioning of any system in place. Change being the only constant, companies need to devote time to strategizing planning and executing their move so that it positively affects each and every person in the organisation.
ImpactQA’s ERP testing solutions offer unique methodologies and a holistic approach to tackle enterprise software testing for every business type. Through our cutting-edge QA services, we provide customised solutions for your end-to-end ERP testing projects starting from test planning, strategies, and test preparation to test management, coordination, and implementation.
Contact our executives to get a free consultation for your next ERP project.